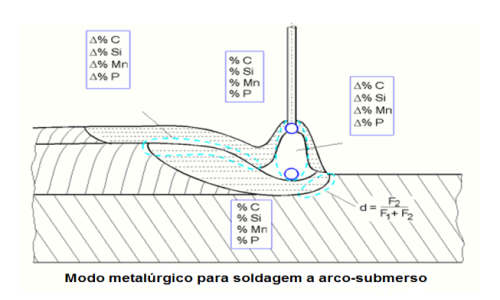
N muitos casos são importantes para estimar ou mesmo para calcular a composição química do metal de solda antecipadamente. Se o metal de base e o metal de enchimento (mais precisamente o metal de solda puro) têm uma idêntica composição, a cada passe de solda terá a mesma composição química e não o contrário. Na figura seguinte são mostrados os principais processos para a composição química
do metal de solda.
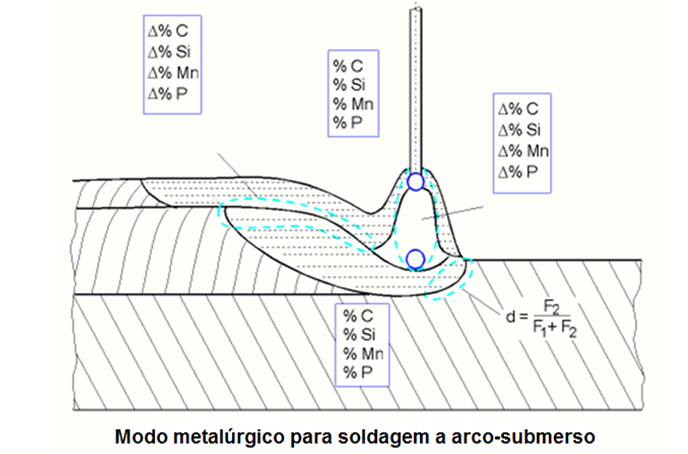
A concentração do elemento X em % de peso no metal de adição é X, fm
. Na ponta do arame eletrodo é fundido uma gota. Esta gota reage com o fluxo fundido e também com a atmosfera de gás na (caverna). A mudança na transformação do elemento x é x, e então a gota ao entrar no banho metálico terá um conteúdo Xdr = Xfm + x. O valor de X pode ser positivo ou negativo (ganho ou perda).
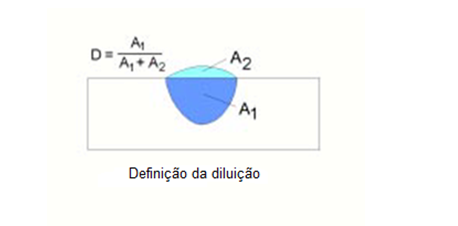
A diluição com o metal de base é definida como mostrada na imagem à esquerda. Os valores possíveis da diluição são entre 0 e 1, ou seja, 0% e 100%.
A composição química do metal de solda do 1º passe em relação ao elemento X consequentemente.

O metal de solda puro é idêntico com a composição das gotículas durante a soldagem, portanto, podemos dizer que o metal de solda puro está presente durante toda execução da solda e que a composição química da solda é a mistura destas gotas e do metal de base ou passes anteriores. Isto é fica claro então, que em soldas de múltiplos passes sua composição fica entre dois limites: metal base e metal de solda puro
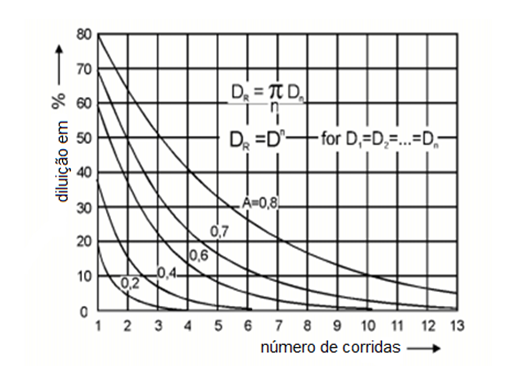

No caso pratico não precisa de uma infinidade de números de passes para preparação do metal de solda puro, mas somente alguns passes que resultam da diluição do metal de base mais cerca de 1 % na soldagem à arco-submerso, com parâmetros que tenham diluição a cerca de 60 % a cada passe. O número de passes é mostrado no diagrama.
No caso pratico não precisa de uma infinidade de números de passes para preparação do metal de solda puro,

Para evitar que o metal de solda liquida corra para baixo ou ambos os lados, esquerdo e direito da amostra estão posicionados dois pedaços de ferro e o espaço da amostra preenchido com o fluxo de soldagem utilizado.
Depois de soldar a mais alta camada análises químicas são determinadas. Ganho ou perda de elementos e diferenças do metal de enchimento são analisadas.
Com este teste qualquer mudança no que diz respeito ao fluxo pode ser verificada, porque qualquer mudança no fluxo provavelmente também afetará reações metalúrgicas de diferentes elementos.
Este metal de solda puro é adequado apenas para a determinação da análise química. Não é adequado para a determinação das propriedades mecânicas. Isso ocorre porque a taxa de resfriamento é muito mais rápida do que na solda propriamente dita. Para as propriedades mecânicas do metal de solda usamos o metal de solda de acordo com a norma DIN 1913, mas tudo isso contem no metal de solda mais ou menos 10 – 15% restantes de diluição com os metais de base usados no lado direito e esquerdo.
Se acompanharmos a composição química do metal de solda emergindo vários passes de solda durante a soldagem, obtemos um diagrama como o da esquerda. Porque usamos como metal base o aço 1.4301 depois de 10 passes alcançou-se o metal de solda puro. O ganho ou perda de níquel é zero, enquanto o fluxo não contém partículas metálicas de níquel. Sob as condições utilizadas há uma perda de cromo de aproximadamente 0,8 %. Nióbio também mostra uma perda e silício mostra um ganho de fluxo.
Os parâmetros de soldagem também têm uma influência sobre o ganho ou perda de elementos. Isso é mostrado no diagrama à esquerda para tensão.
A explicação mais simples do efeito da tensão de soldagem é que, com o aumento da tensão de soldagem o arco se torna mais longo. Este aumento de tempo de reação na gota, estado para que um ganho ou perda é aumentado um pouco.
Com o aumento da corrente de soldagem torna-se mais curto o arco e também o tempo de reação no estado das gotículas diminui. Portanto, ganho ou perda reduz e a corrente aumenta.
A velocidade de soldagem não tem influência no ganho ou perda de elementos, porque não há nenhuma mudança de reação nas gotículas.
Com fluxos de soldagem que contém partículas metálicas em seus elementos de liga, no entanto, a velocidade mostra um efeito. Isto porque as partículas metálicas fundidas na escoria entram no banho metálico, assim este mecanismo é afetado pela soldagem.
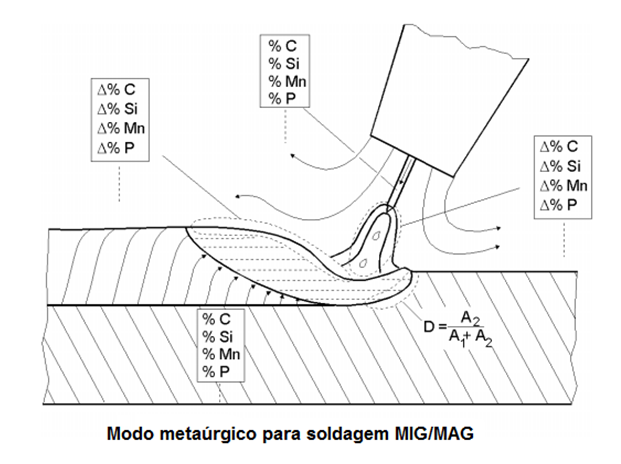
Experimentos com MIG-MAG – soldagem também mostrou que a reação do banho pode ser negligenciada. Podemos calcular com as mesmas equações derivadas antes para arco submerso.

Para experimentos MIG-MAG – para a soldagem descrita abaixo os gases de proteção listados na tabela a esquerda foram usados.
Note que as designações da tabela da esquerda não correspondem aos utilizados na EM 439.
A primeira observação durante a soldagem MIG-MAG foi uma influência do gás de proteção com sobre a diluição com o metal base.

Uma influência tão grande não era esperada antes.
O ganho e a perda de elementos encontrados estão listados na tabela a seguir.

Com o aumento de oxigênio contido no gás de proteção houve perdas de elementos de liga em vincos.
Se o gás de proteção contem CO2 um ganho de carbono é observado. Isso porque o CO2 no arco é dividido em átomos e assim pode facilmente ser transferido para o banho metálico.
Consequentemente ligas de alta resistência corrosão não devem ser soldadas com CO2 – contido no gás de proteção. O teor de carbono cada vez maior contido no metal de solda tem consequências negativas como é mostrado abaixo.
Ao traçar o diagrama a seguir a pergunta era: qual variável independente para o eixo X – deve ser usada para diferentes gases de proteção.
A partir de um ponto de vista metalúrgico é claro, que o CO2 em altas temperaturas as gotas se quebram de acordo com a reação abaixo.

Então a partir de duas partes de volume de CO2 três partes de volume de gás são formadas com uma parte de O2. Isto foi levado em conta para o cálculo do teor de oxigênio livre dos gases de proteção. Este conteúdo foi utilizado para o eixo X.
Em relação ao conteúdo de carbono a estabilização é proporcional ao metal de solda, no entanto, é necessário olhar separadamente o CO2 contido nos gases.
A imagem a esquerda mostra que um ganho de carbono leva a diminuição da relação de estabilização do metal de solda. Sendo isto prejudicial ao metal de solda.


O ganho e a perda de elementos de liga durante a soldagem MIG-MAG também muda a localização do metal de solda no diagrama de Schaeffler.

Isto significa também que o conteúdo de ferrita é alterado como o diagrama a esquerda mostra.
Argônio – misturas de oxigênio mudam apenas um pouco o metal de solda e o conteúdo de ferrita não muda. Sob CO2 – contendo gases de proteção, no entanto, o ganho de carbono desloca o metal de solda para um conteúdo mais baixo de ferrita. Isso pode levar a uma solidificação austenítica com o perigo de trincas.
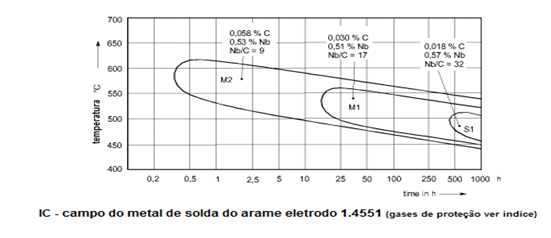
O diagrama a esquerda mostra os campos de IC dos metais de soldagem em diferentes gases de proteção. O metal de solda feito com o uso de Argônio S1 precisa de um tratamento térmico de cerca de 500 h, 500ºC para se tornar um IC propenso ao metal de solda.
O ganho de carbono por meio dos gases de proteção M1 e M2 levam a mudança de IC para campos de tempos mais curtos. Isto não é procurado em tudo, porque um tratamento térmico de alivio de tensões pode levar rapidamente a um IC susceptível ao metal de solda A situação do planejamento de uma junta soldada é mostrada a seguir, no diagrama de Schaeffler.
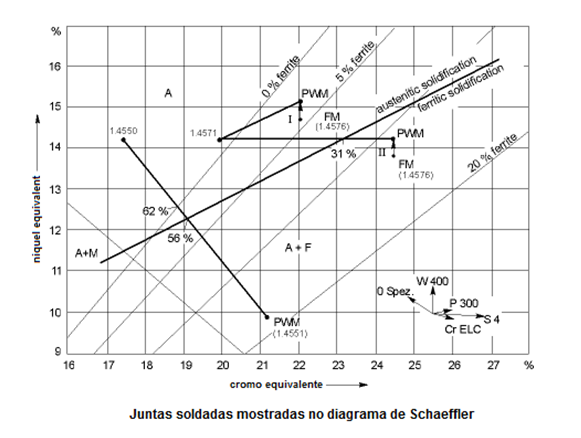
Todas as soldas executadas devem estar localizadas abaixo da linha de fissuração a quente.
O primeiro exemplo mostrado na parte esquerda do diagrama é uma solda TIG em um aço1. 4550 com um metal de solda correspondente 1.4551. A real composição química foi levada em conta para calcular os pontos mostrados no diagrama. Pode ser visto que a diluição com o metal base deve ser inferior a 56%, caso contrário o metal de solda terá fissuração a quente.
O segundo exemplo é uma junta soldada de chapas de aço de 1, 4571 de espessura e fluxo e arame nas combinações I e II. O diagrama mostra que a combinação não é adequada, porque a trinca a quente não pode ser evitada. A combinação II não é adequada para qualquer execução de raiz porque a diluição seria de cerca de 80%. Se a raiz é soldada com uma vareta de eletrodo adequada à combinação II pode ser usada para a seguinte execução.
Para uso do diagrama de Schaeffler, os ganhos e perdas de um fluxo determinado podem ser calculados em termos equivalentes ao diagrama de Schaeffler e ser rebatido ao diagrama como o vetor de fluxo.
Esse texto foi traduzido por alunos da fatec-sp
torne-se um engenheiro ou um especialista internacional de soldagem IIW IWE IWS
Entre em contato por: +55 (11) 91713-0190 / 96378-0157 / treinasolda@infosolda.com.br / Infosolda@infosolda.com.br